Today, we will look at different options we have for temperature sensing. To try and understand the strength and weaknesses of each method. By the end, we will figure out which technology is right for a given use-case in this brief guide to temperature sensing.
A Brief Guide to Temperature Sensing
The following list doesn’t include temperature sensing devices/methods which cannot be in the product, like infrared temperature measurement.
Options we have are:
- Thermistors
- NTC
- PTC
- Thermocouple
- RTD (Resistance Temperature Detector)
- Temperature sensing ICs
- Digital Output
- Analog Output
- Thermostats
1. Thermistors
Thermistors are a two-pin device that changes their resistance according to change in temperature. Generally, used to measure temperature in the -100°C to 500°C range.
If the thermistor’s resistance increases with an increase in the temperature, it is called PTC or Positive Temperature Coefficient thermistor.
Similarly, if the thermistor’s resistance decreases with an increase in the temperature, it is called NTC or Negative Temperature Coefficient thermistor.
Thermistors are the most cost-effective solutions to do rudimentary temperature measurements. They have a fast and non-linear output. These are not highly accurate sensors but can perform well when used in smaller ranges. They can produce large resistance changes for a slight temperature variation. The output of a voltage divider formed using a thermistor gives use a temperature dependent voltage output. Sensor self-heating needs to be taken care of during measurement.
2. Thermocouples
In thermocouples, we use the Seebeck effect to measure temperature.
Thermocouples are made-up of two dissimilar metals, and their classification depends on the metals used for their construction. Few common types are K, T, R, S, etc.
Different types of metal produce different output curves and have different operating temperature ranges. Generally, used to measure temperature in the -200°C to 2500°C range.
Thermocouples are rugged and used in a hazardous environment. Self-heating is not an issue as it does not require an external power source. Temperature sensing is fast due to its low thermal mass. They are more accurate than Thermistors but are less accurate than RTD (more about it shortly). Thermocouples require a considerable amount of signal processing. They also need cold side temperature reading for compensation in high accuracy temperature measurement.
3. RTD (Resistance Temperature Detector)

Similar to a thermister, RTD’s resistance changes with temperature, but RTD has a linear response. Its linear temperature response makes temperature measurement with RTD highly accurate. RTDs can be used to measure temperature in the range of -200°C to 850°C. They come in various forms and shapes, which makes them more versatile. Though RTDs are accurate, working with RTD is a bit tricky. The change in resistance per degree Celsius is small, so it needs excellent low noise amplifiers.
The accuracy of the temperature sensing when using RTD depends on the drift of the current source. But there are circuit topologies that can compensate for the drifting of the current source. For a higher signal-to-noise ratio, you would like to have more current going through the RTD to produce a higher voltage drop. But a high amount of current flowing through the RTD also leads to self-heating. Thus it is a balancing act of voltage drop across RTD and gain needed for accurate measurement.
Various industries used RTD heavily due to its versatility and accuracy.
4. Temperature sensing ICs
As its name suggests, they are temperature sensing ICs. They are used to measure onboard temperature within the range of -20°C to 150°C. You will find such ICs on your computer RAM to measure heat dissipation. These ICs have two types of output digital or analog. These types of ICs are also used with thermocouples at the cold junction to improve their accuracy.
5. Thermostats
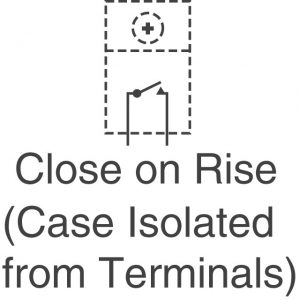
Thermostats are switches that turn on/off at a set temperature. These are handy components designed for a specific operation. They generally don’t provide any reading when the temperature changes.

For example, I want to turn on a fan blowing over a heatsink when the heatsink’s temperature goes above 50°C. I will use a thermostat that is normally-open and closes when the temperature exceeds 50°C. Using thermostats makes the systems extremely simple, so the system has fewer failure points. Compared to a thermistor-based circuit arranged in voltage divider configuration with voltage sensing and switching elements like a transistor, the thermostat reduces the number of components making assembly cheaper, make the systems easy to maintain.
All done! We have gone through most of the commonly used components for temperature measurement. Though this is quite a simple explanation of each element, you hopefully now have a better understanding of which device to use for a given application concluding our brief guide to temperature sensing.